Signs That You Have Quality Control Issues in Your Business
Quality control is crucial for any business that aims to satisfy its customers and maintain a good reputation. When things go wrong with quality control, it can lead to unhappy customers, wasted resources, and a damaged brand that might be hard to recover.
This post will help you identify some common signs that your business might have quality control issues. Recognizing these signs early can save your business from bigger problems down the road.
Frequent Customer Complaints
One of the most obvious signs of quality control issues is frequent customer complaints. If your customers are regularly reporting problems with your products or services, it's a clear indicator that something is wrong. For instance, if a manufacturing company frequently receives complaints about defective products, it suggests that there may be flaws in the production process.
Listen to your customers carefully. They are often the first to notice when something isn't right. Pay attention to recurring themes in the complaints, as these can point to specific areas that need improvement.
Production Delays
Frequent production delays can also indicate quality control problems. If your production line is constantly stopping due to issues that need fixing, it's a sign that something in your process is not working correctly. Delays can be caused by faulty equipment, poorly trained staff, or problems with raw materials.
Addressing production delays promptly is crucial. Not only do they disrupt your workflow, but they can also lead to missed deadlines and unhappy customers. Identifying the root cause of delays can help you improve your overall quality control.
High Return Rates
If you notice a high return rate for your products, it's a strong signal that there are quality control issues. High return rates can mean that your products aren’t meeting the expectations or needs of your customers. For instance, if an industrial hose manufacturer sees a spike in returned hoses due to leaks or defects, it indicates that the production process needs closer scrutiny.
Track your return rates over time to identify patterns. A sudden increase in returns can help you pinpoint when and where things started to go wrong.
Inconsistent Product Quality
Inconsistent product quality is another red flag. Your customers expect a certain level of quality every time they purchase your product. If they receive products that vary widely in quality, it can damage their trust in your brand. For example, if one batch of products is excellent, but the next is full of defects, it suggests that your quality control processes are not being followed consistently.
Ensuring consistency requires strict adherence to quality control standards at every stage of production. Regular inspections and testing can help maintain consistent quality.
Increased Waste and Rework
An increase in waste and the need for rework is a clear sign that your quality control processes are not effective. When a significant amount of your production ends up as waste or needs to be reworked, it means that mistakes are being made that could have been avoided. For instance, if your team frequently has to rework products due to incorrect specifications or defects, it suggests that there’s a lack of oversight or proper procedures in place.
Minimizing waste and rework not only saves money but also ensures that your products meet the necessary standards before they reach your customers. Implementing more rigorous quality checks and training for your staff can help reduce these issues.
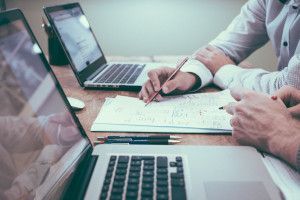
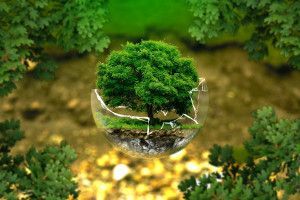