Common Types Of Manufacturing Waste And How To Avoid Them
For any manufacturing process to be truly efficient, it’s important to find ways to eliminate or, at least, reduce
manufacturing waste
. This type of waste is any action in the manufacturing process that does not benefit the customer or add value to the product. Manufacturing waste can cost a business a significant amount of money, from defective products to transportation waste. And yet, it’s one aspect of the manufacturing process that many businesses overlook. Here are some common types of manufacturing waste and what you can do to avoid them.
- Defects
Defects in manufacturing
occur when the product is not manufactured properly and falls short of its intended design. And what happens with most companies is that almost all defective products are discarded, costing money, wasted time, wasted energy, and of course, wasted product. For example, a prescriptive drug or a gummy chewable may become contaminated through the manufacturing process or may break or lose its shape due to a sub-standard manufacturing process. To avoid this, it’s important to reevaluate your product design, create a flexible manufacturing process, and ensure effective quality control and inspection processes. You should also invest in a high-quality manufacturing process and products. For example, if you produce gummies, then it’s best to invest in premium quality molds and a
gummy machine
. This way, you can minimize the risk of broken or inconsistent shapes in the manufacturing process.
- Transport waste
Transport waste occurs when material movements do not directly support or lead to immediate manufacturing, which can happen in several ways. For example, if your manufacturing facility has an improper layout, poor scheduling, or poor production planning, you can easily create transport waste.
Transport waste
can also happen when a product used in manufacturing is moved about unnecessarily. It could occur when transporting raw materials from a supplier to the manufacturing plant. And it can lead to products being damaged or even misused. To reduce transportation waste, it’s important to find ways to shorten the supply chain, create an effective layout, and work schedule.
- Excess processing
Excess processing happens when you provide more value in a product than your customer needs or requires. Also known as over-processing, it can cost your business some level of financial burden when you invest more-than-necessary material and staff time required to make a product. A good example of excess processing waste happens when a portion of a product is more highly polished using machine and labor when it is not a functionality requirement for the customer.
- Waste of waiting
Waiting waste refers to an inventory that is sitting idle, whether on waiting shelves or between manufacturing stations. And this can cost your business lots of money and time. A typical cause of waiting for waste is unplanned downtime. That can be caused by production bottlenecks, extra long setups, and poor condition of facility equipment. To minimize or eliminate waiting waste, you can consider redesigning your manufacturing process or shortening it to ensure a single piece and production flow. You can also find ways to standardize employee training, processes, and instructions.
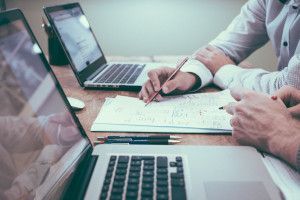
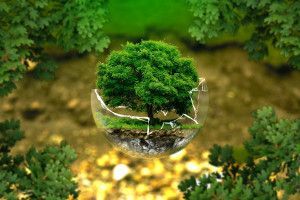