Improving The Performance of Your Machinery for Increased Quality and Output
As a business owner, you likely know that the key to output and quality standards is to ensure that the machinery you use is in top condition and can handle the workload.
What might not be so obvious is the best way to approach the care and maintenance of said machinery to get the most from it and reduce high-quality, consistent results. In reality, poorly maintained machinery or machinery that is past its best isn't always cheaper; in fact, it costs you more in the long run in terms of repairs, replacement parts, reduced output, and increased mistakes.
If improving the performance
of machinery within your business is a high priority for you, read on for some tips on how to move forward and ensure you're working at full capacity and your machinery can cope with your business's demands.
Regular Maintenance
By implementing a regular maintenance program, you can regain control over your workflow and avoid the chaos of unexpected downtime. This proactive approach not only ensures that all care and repairs are managed, preventing unplanned downtime but also provides a sense of stability, allowing you to maintain a regular output without disrupting your processes.
Implement a schedule that includes having experienced professionals regularly check and service all machinery, identify potential issues before they become massive problems, and put measures in place to ensure each piece of machinery is performing at its best and has the right parts it needs to avoid breakdown of quality concerns. On top of this, an effective repair reporting portal should be in place so operators can log any concerns and have them addressed promptly.
Correct Usage
Empower your team by ensuring they are fully trained and aware of how to use the machinery. This can significantly reduce the need for repairs or breakdowns caused by incorrect use. By implementing practical training and protocols, you can ensure everyone follows guidelines set by the manufacturer and the company, keeping everyone safe and removing the risk of inappropriate use.
To back this up, all instances where employees are knowingly flouting rules and usage guidelines need to be dealt with swiftly, either by further training or consequences such as employment termination.
Optimize Setup
If you don't set up equipment and machinery in a way that makes sense for their use, this can impact their use and place more pressure on the employees and the equipment itself. You need to look at the steps and processes that need to be followed to ensure that you assemble them in a way that makes sense and that they're housed and stored correctly for optimal use.
Use High-Quality Parts
Ensuring you use only high-quality parts and the correct parts of the machinery and equipment you rely on is vital. Cutting corners using sub-par quality parts and off brand equipment can cause more damage and render it unusable or decrease quality and output.
As well as ensuring you use only certified engineers for repairs and have a robust maintenance schedule in place, you need the right parts designed to benefit your machinery and last. Whether this is thermoplastic PEEK valve plates or using manpower-recommended service engineers, follow the rules to ensure you don't cause any unintentional damage and feel secure about the reliability of your equipment.
Increase Automation
Increasing automation means that there is less human involvement and fewer instances where things can go wrong. Suppose it is able to integrate automation into your machinery to enable it to operate efficiently. This can help you improve performance and get the most from the equipment. This isn't possible for all machinery, especially those that specifically need to be operated manually however by looking at how you automate some aspects of your machinery, even if it's just for minor usage and performance, the more you can see how you can make improvements, and limit problems, and damage.
Identify Bottlenecks
Are there specific places your team is getting stuck or processes that are backing up or not working well? If you are repeatedly hitting issues, it's crucial to take a step back and look at the bigger picture. This proactive approach will help you identify and address bottlenecks, making you feel more in control of your operations.
Follow the path from beginning to end; assess each piece of machinery's part in the process and how it performs in conjunction with other operations and equipment you use and human interaction. From here, you can identify issues, reconfigure your processes, and improve your performance by removing bottlenecks or implementing initiatives to reduce the impact.
Monitor Continuously
Continuous monitoring might seem like overkill, but if you don’t know how things are performing when issues are occurring, and what prevents or is a precursor to problems, you can't even consider making improvements because you don't have a starting point. Even if you don’t experience issues, ongoing monitoring for performance and output, can alert you to changes you might need to make in the future or identify things you can improve on. On top of that, continuous monitoring gives you a better idea of the health and efficiency of your business so you can continue to build on what you do to make things better all the time to meet demand and identify changes.
Standardize all Processes
To really get the most out of your machinery and your employees, you need to have standardized processes across the board. You need constancy, a checklist that everyone follows, and the familiarity this brings can enable you to ensure that everything is running correctly and that you are maximizing output. These protocols and processes might take some time to become second nature but, in time, as people get used to doing them, you will notice a sharp uptick in personnel efficiency and the efficiency of your machinery and equipment.
In conclusion, implement an effective training plan for all employees, monitor processes and output efficiently, use high-quality parts, implement regular maintenance and service, and be aware of any issues and bottlenecks that affect the performance of your machinery and employees to help you restore and retain functionality.
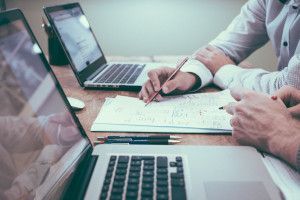
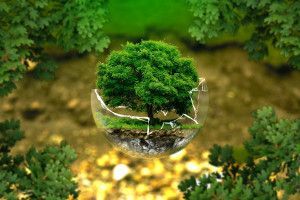